how SES-6 works is explained in 140 seconds
rotary actuator compactly summarized
Find out for yourself why a pneumatic rotary actuator from Wagner moves so precisely to the end position or how the swivel angle is set. The animation shows, among other things, our integrated air feedthrough, which is also available in the SE and SM series. In the cross-section through the milled, high-strength aluminum housing, you can see how shock absorbers (hydraulically) cushion the rack of the swivel module. We visualize how the signal is guided through the rotating shaft. Another hidden advantage for your application:
The shock absorbers are deliberately on the same side as the stop screws. If you screw the electrical sensor into the hollow screw, all the interference contours are on one side! This gives you degrees of freedom and allows you to use it in tight spaces. Milling for a C-slot sensor is also available as an option.
The SES series shown delivers a high torque of 24Nm at 6 bar in the largest version (size 9).
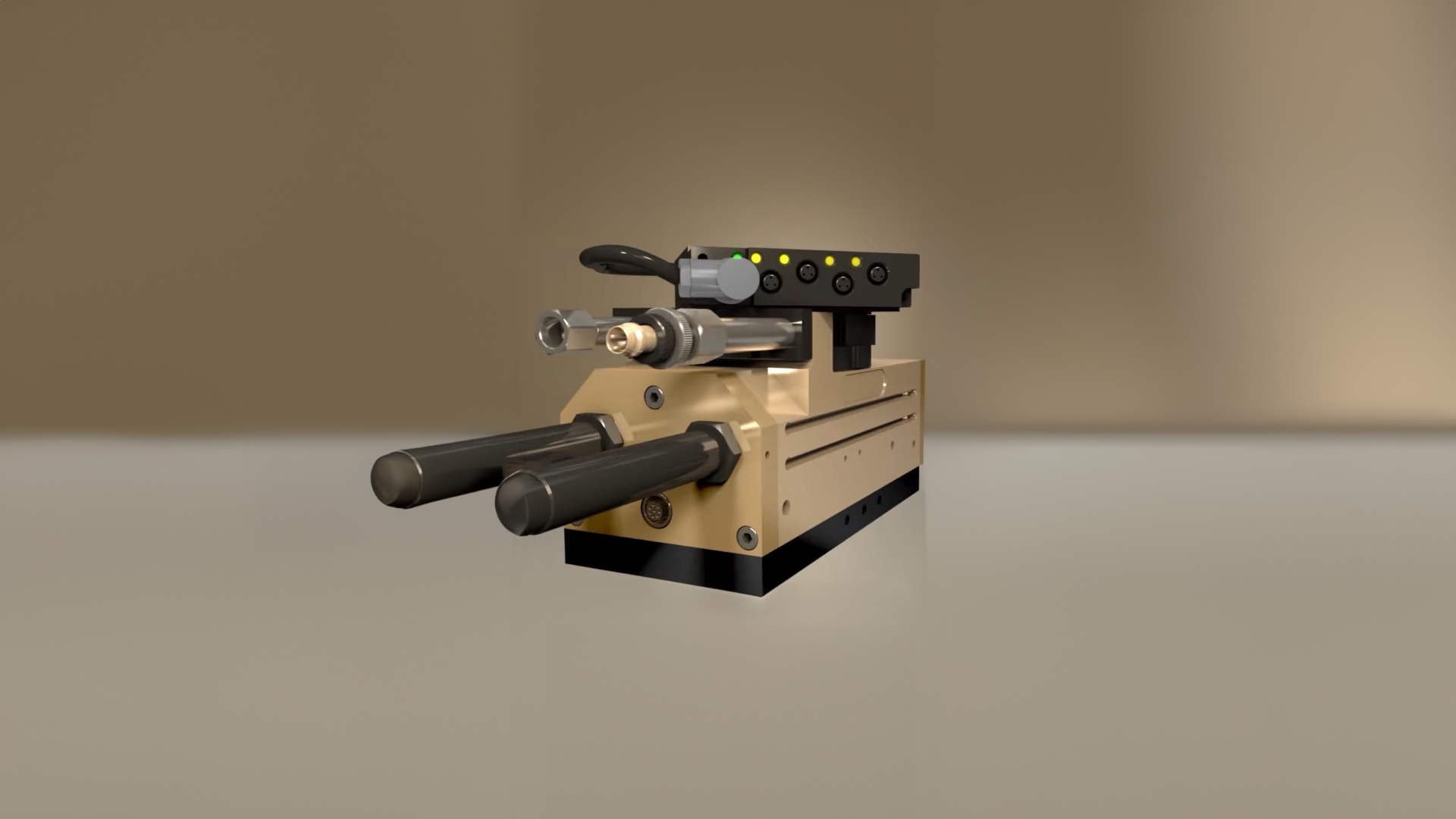
downloads
NOTE: OUR DOWNLOADS ARE MAINLY AVAILABLE AS PDF FILES. YOU WILL NEED THE LATEST ADOBE ACROBAT READER TO READING THEM.
Angle of rotation adjustable from outside!
Friedemann Wagner GmbH enables the user to adjust the angle of rotation using a stop screw . Screwing in the screw limits the path and thus the swivel angle - and vice versa. This is advantageous for the user! With one product variant, the required swivel angle can be set between 0 and 190° .
Therefore, the number “190” always appears in the module designation - as in the swivel unit SE-4-N-190-K-0-0 P.
The stop screws are clamped after the angle has been set. They are hollow to accommodate inductive sensors . This saves valuable space and avoids additional interfering edges.
Depending on the customer application, “K” or “H” versions can be selected. The H version has two hydraulic shock absorbers fitted at the factory.
Example:
- SE-6-N-190-K-0-0-P = no damping
- SE-6-N-190-H-0-0-P = hydraulic damping mounted upon delivery
It is of course possible to retrofit the dampers at a later date!
Read below how we, as a long-standing manufacturer, have gradually improved the rotary actuators since the "SHE" version series! We also offer rotary actuators with full power in the end positions. Curious?
Choose from different sizes and designs – also using the filter function offered!
pneumatic swivel unit
Technical data, the 3D model as well as links to the brochure and operating instructions can be found directly in the product selected below.
Further information can be found in the central download area , under the FAQ section, our blogs or our YouTube channel.
intermediate position rotary actuator
A pneumatic module basically has two defined end positions.
In the swivel drive, these are limited by the set swivel angle .
We offer additional modules for various rotary actuators, so-called intermediate positions. These modules are coupled to the relevant basic product. They allow a third position - adjustable within certain limits - despite pneumatics.
Technically, it is an additive cylinder that “moves” into the swivel drive when activated and limits the travel of the racks of the base unit.
Possible application examples are
- central workpiece holder for optical inspection for correct positioning
- elimination of a "bad part"
Evolution of the rotary actuator
As a manufacturer, we have continuously pushed forward the technical improvement of rotary actuators for the benefit of our customers.
A rotary actuator of the SE, SM or SES variant has external stops and offers full torque in the all-important end position. The user can mount his additional modules on the swivel surface of these variants - centering holes, grid dimensions and threads are already included!
Wagner rotary actuators have housings made of milled, high-strength aluminum - the external stop is part of the housing. Depending on the load structure and throttling, dampers can be completely dispensed with - this affects the purchase costs and maintenance costs of your automation.
External stops show the physical advantage in the repeatability of +/- 0.01°. In our design, repeatability depends on the clamped stop screw on the external stop and not on the play of the gearing.
We also shift the impulse load of each cycle: away from the rack and towards the stop surfaces of the external stops. Together with the lower forces on the stop screws (force diagram), the benefit is obvious: longer service life, fewer production interruptions.
Since the damper, stop screws and the sensors that can be inserted there point in one direction , all other sides of the rotary actuator are free. This is advantageous in tight installation situations.
Initial assembly, commissioning and maintenance benefit from this accessibility, especially since the swivel angle can be adjusted from the outside by screwing in/out! After adjusting the screws, the system is fixed with a clamp.
The hydraulic dampers of the swivel unit are also accessible from the outside, making adjustment and replacement easier.
Clever solutions for air feedthroughs in the stop surface save valuable space and costs in the application. They are implemented compactly in the rotating shaft: short distances, no torsion! Our mini rotary actuator SM-4 with air feedthrough to the mounted mini gripper makes a good impression.
From size SES-6 (due to size) the sensor signal can even be connected to our connector strips and brought through the shaft to a socket on the front of the swivel unit.
A third position is achieved using an additional module. This intermediate position is docked to the swivel drive instead of the rear plate. Technically speaking, this is another cylinder that stops the unit in the middle of the swivel cycle (at +/- 90°, adjustable) by pushing the racks out of their end positions.
Applications? Think of the delivery position of a rejected part, or even the start of the cycle: pick-up in the middle - swivel to the left or right depending on the correct position. As an available additional module, this function can also be retrofitted to an existing swivel unit if required. We see this as sustainability in action!
In order to avoid having to screw in the screws too far at small swivel angles , the customer can also move the stop blocks - corresponding holes are available.
As a special function, our design principle enables the detection of a shock absorber failure . Use the real query of the end position. Avoid subsequent costs for the workpiece, device or system due to defective shock absorbers
Conclusion: Since the first part-turn actuators in the SHE series (original product name "SEN"), there has been a constant improvement based on customer feedback, which is reflected in the current SM, SE and SES solutions. Of course, part-turn actuators in the SHE series are still available as cost-effective solutions in two sizes. And these have also received the hollow stop screw for screwing in the proximity switch over time.
Conclusion: Since the first part-turn actuators in the SHE series (original product name "SEN"), there has been a constant improvement based on customer feedback, which is reflected in the current SM, SE and SES solutions. Of course, part-turn actuators in the SHE series are still available as cost-effective solutions in two sizes. And these have also received the hollow stop screw for screwing in the proximity switch over time.
We look forward to hearing from you
Personal advice
Friedemann Wagner GmbH
Robert-Bosch-Str. 5
D-78559 Gosheim
+49 (0) 7426 / 949 00 -0
+49 (0) 7426 / 949 00 -9
E-Mail schreiben